Surface Finishing
Our Capabilities
Surface Finishing
Once a structural part has been die-cast,its important to note,the process is not necessarily over.The process of die casting and subsequent die casting finishes have a symbiotic relationship,they are heavily dependent upon each other and they work together to create the final product.In fact,there are a large number of die casting finishes for us to choose from-all of which are intended to improve the aesthetic and functional characteristics of your component.These include everything from adding a decorative touch to the product to improving its chemical or corrosion resistance.Thus for us it is crucial to ensure that our product does exactly what it was intended to do.We offer an extensive range of post-casting finishing procedures.
Surface Finishing
design process
- Trimming & Fettling : The final step in the die casting process is trimming. While the metal is cooling, the excess metal in the sprue and runner must be removed along with any flash that has transpired. This extra material is then trimmed away from the final casting. Fettling is a process of removing excess material from castings often formed by the die's parting lines during the casting process when molten material is injected into the die/mould
- Vibratory Deburring: Our metal finishing services include vibratory deburring that can effectively remove sharp edges and other imperfections from the surface of the product. Deburring can also prepare the surface for painting and other finishing processes, as well as improve the product’s aesthetic appeal.
- Shotblasting: Another commonly used die cast finishing process is shotblasting, which involves the high-speed projection of steel particles to clean or strip the surface. Commonly applied shot blasting techniques include airblasting and wheel blasting.
- Powder Paint: Powder painting, which is also known as powder coating, involves the application of an organic powder that achieves paint adhesion through electrostatic attraction. Powder painting offers maximum efficiency and is also friendlier to the environment than solvent-based painting methods.
- Wet Spray Paint: Our metal finishing company can precisely execute traditional wet spraying processes that are extremely beneficial in a wide range of industrial applications.
- Plating- Chromate, E-Nickel, Cadmium, and Silver Plating: Electroplating is the process of depositing metal ions onto the surface of a product via electrodeposition for purposes such as increasing corrosion resistance and enhancing aesthetic appeal. We can provide plating services using various types of metals.
- E Coating: Electrophoretic painting, also known as e-coating, is somewhat similar to electroplating, except that paint is electrodeposited onto the surface instead of metal. Our metal casting services include an effective e-coating process that is often preferable




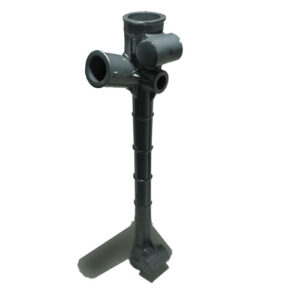
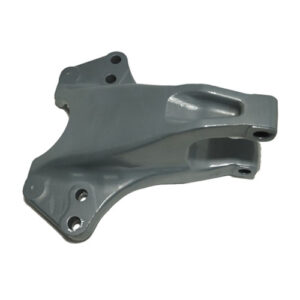


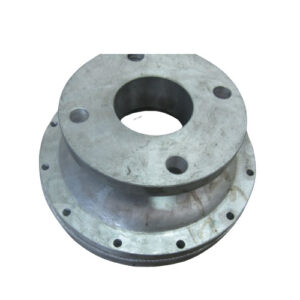


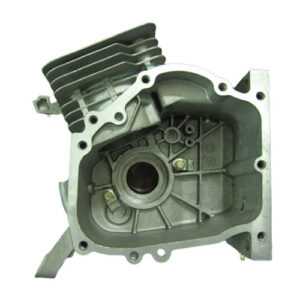



