Low Pressure Die Casting
DIE CASTING
LOW PRESSURE DIE CASTING
Low pressure air is introduced into a sealed furnace holding a tank of molten metal. The metal feeds up slowly through a riser tube and into the die cavity. Once the casting has solidified in the die, air pressure is released, allowing any residue molten metal still in the riser to fall back into the tank for recycling. When cooled, the casting is removed.
LOW PRESSURE DIE CASTING
Manufacture
- Metal is displaced from the furnace and forced up the riser tube using air at 20–100 kN m-2, or by evacuation of the mould. “Counter-pressure die casting” is a variation in which the mould is filled by having less than 1 millibar pressure differential produced by controlled leakage from the mould. This slow, smooth and progressive filling of the die cavity reduces metal turbulence and gives temperature gradients which are favourable to feeding, thus producing sound, high-quality castings.
- Dies are usually cooled between castings, using air or water sprays and have die-coatings.
- Sand or shell cores can be used in the dies to produce internal cavities, but usually require a refractory coating to prevent metal penetration under pressure.
- Castings have no runners or feeders in the true sense, and hence high yields (80–90%) and low remelt ratios are obtained which, coupled with reduced fettling, gives a high energy saving.




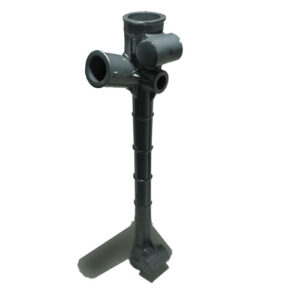
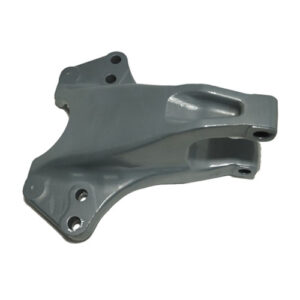


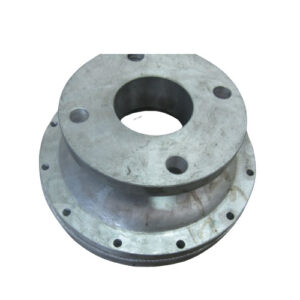


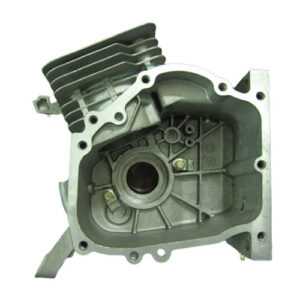



