Pressure Die Casting
DIE CASTING
PRESSURE DIE CASTING
High pressure die casting is the process of injecting molten metal into a steel die under pressure (eg 1,500 PSI). The metal is poured into the die casting machine either by hand using a ladle or by a robotic arm. A piston then fires the metal into the mould. Once the metal has solidified the casting is ejected and taken out of the machine by the operator or by a robotic arm. Due to the thinner wall sections there is a quicker solidification time and much higher production rate than gravity die casting. Therefore it is usually associated with high volume parts. It is suited to die castings which require high dimensional accuracy and a good surface finish. Due to the accuracy that is achievable any secondary machining operations can be kept to a minimum. Castings can be made with thinner wall sections than sand or gravity castings while still providing high strength.
Our focus is on providing our customers with competitive prices while maintaining the highest quality possible. This is achieved through our lean manufacturing program and extensive work instructions to ensure control over every process. Although high pressure die casting is geared towards high volume we also specialise in smaller to medium quantities delivered to our customers schedules. Due to the environments many of our high pressure die castings are used in only the best quality of metal is sourced. Certificate of conformances are issued with every delivery of metal along with a chemical analysis. We are then able to offer full metal traceability from the melt number to finished die casting.
ADVANTAGES
PRESSURE DIE CASTING
- High production rates achievable
- High strength
- Thin wall sections eg 1.5mm – 2mm
- Excellent tolerances & properties repeatable
- Best surface finish possible




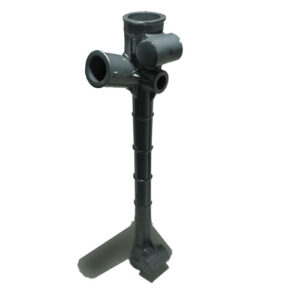
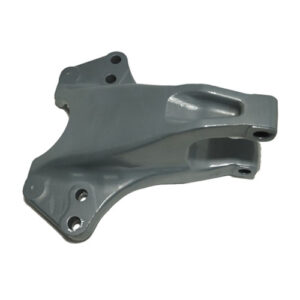


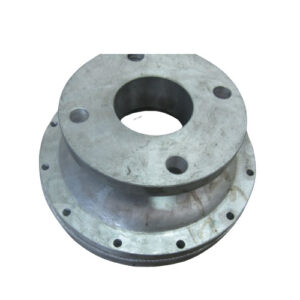


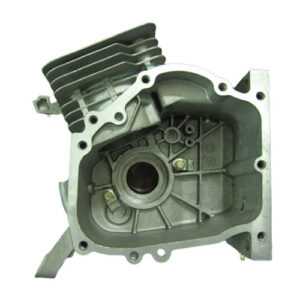



